Post Tensioning Industry
2024/5/6 2:31:35
The bridge construction environment is generally complex. The application of post-tensioned prestressed concrete box girders can effectively solve the problem of large environmental interference, that is, the box girders are applicable in a variety of environments. The post-tensioned prestressed concrete box girder is an indispensable part of the whole bridge, and the construction work of this part should be completed in a reasonable way.
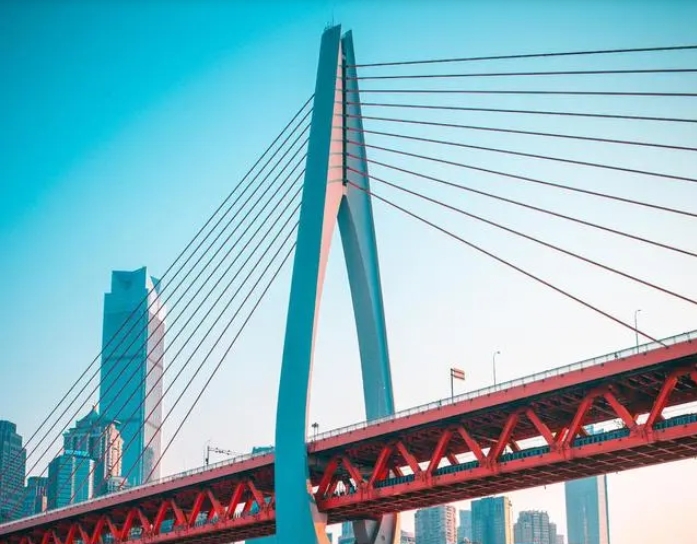
1Project Overview
The total length of the interchange ramp bridge at a certain hub is 432m, and it adopts a 4-link layout (4m×30m+4m×30m+2m×32m+4m×30m). In terms of structural composition, the superstructure is a single-box, double-chambered structure, both equipped with prestressed concrete cast-in-place continuous box girders. The size control standards are top width 1050cm, bottom width 750cm, and top and bottom plate thicknesses of 25cm and 22cm respectively. Taking the bridge deck construction requirements as a reference, the transverse and longitudinal slopes of the box girder are the same. The pier bearings directly affect the construction status of the cast-in-place box beams, and basin-type rubber bearings are planned to be used.
2 Main contents of prestressed construction
2.1 Installation of prestressed bellows
Configure prestressed pipes according to the construction requirements of this project. Plastic corrugated pipes are uniformly used. They are installed in place in sequence according to the construction drawings. Through spot welding of U-shaped ribs and positioning ribs, the stability of the corrugated pipes must be ensured without any To prevent burn phenomenon, the distance between straight sections is set to 100cm. Due to the special construction conditions of curved sections, the distance is reduced to 50cm to ensure sufficient stability of the corrugated pipe. The bridge's steel strands have a large arc, and with the continuous advancement of tensioning operations, concrete collapse is prone to occur. Therefore, strengthening measures need to be taken at the bends of the steel strands, that is, U-shaped anti-collapse steel bars are laid.
2.2 Steel strand installation and single-end extrusion anchor head production
After the corrugated pipe is installed in place based on the drawing, organize the steel strand bundling operation. Before this, the pipe number and length number should be fully considered, and a winch should be configured to exert a traction effect. Adjust the position of the steel strand end so that it is more suitable near the pipe mouth. Properly raise the steel strand bundle so that its end can effectively enter the pipe. There are many hidden points when performing beaming operations on curved parts, so care should be taken to avoid damage to the holes. Comprehensively inspect the stranded pipes. If there is any damage to the joints, repair measures must be taken promptly.
Comprehensively consider the thickness of the anchor clamp, the tensile elongation value, the exposed length of the steel strand, etc., and determine the appropriate cutting size of the prestressed steel bars after many aspects of analysis. Usually, 100cm should be reserved and quickly cut with a grinder. Arc cutting is not allowed during the entire construction process, otherwise the steel strands may be easily damaged.
After braiding the prestressed tendons, insert them completely into the tunnel, and install a mesh sleeve at the front end of the steel tendons to maintain the state of the prestressed tendons and make them straight. To avoid blind piercing, a comprehensive inspection is required. The position of the anchor pad must be reasonable and there should be no blockage in the hole.
3 Main contents of post-tensioning prestressed construction
3.1 Preparation work
(1) Based on the actual measured value of concrete strength, if the value increases to 85% of the design strength and meets the requirement of at least 7 days of age, tensioning operations can be organized under these conditions.
(2) Equipped with intelligent tensioning equipment, technicians will regularly inspect instruments and other components of the equipment to ensure that the equipment maintains stable operation. The measuring range of the pressure gauge should match the working performance of the jack, and all calibration work must be completed by a legal metrology technical institution. Adapt anchors of appropriate specifications according to the characteristics of the tensioning equipment, and strengthen quality inspection when entering the site. If the tensioning equipment is idle for a long time due to construction arrangements and other reasons, a comprehensive verification will be required when it is resumed later. If the jack is used for up to 6 months or reused 300 times, if there are any abnormalities during use, it must be checked in time. In addition, the calibration of the spring dynamometer needs to be strengthened, usually once every two months.
(3) The quality of steel strands should be strictly controlled to form high-strength steel bundles, which are required to have the characteristics of high strength and low relaxation. The standard strength fpk=1860MPa is used as a basis to determine the tension control stress, that is, take this value 0.75 times, from which the control standard can be obtained as 1395MPa. Based on this, the tensile force of a single steel strand can be calculated, that is, F=1395×140/1000=195.3kN.
(4) The tensioning operation follows the principle of symmetry. Tensioning starts from both ends of the web prestressed bundle. Taking the center of the pier as the benchmark, select a position 0.2L away from it on both sides, and set a manhole there to facilitate Complete the tensioning operation of the short beams of the roof at the end, and seal the holes in time after completion.
3.2 Tension process
(1) Complete the tensioning operation in order of the web first and then the roof. Specifically, the web adopts a single-end tensioning method, and the top plate is gradually stretched from the two sides to the middle. Specifically, the single-end alternating tensioning method is selected.
The ramp bridge construction site is located at two places: a gentle curve and a circular curve. The length of the prestressed steel tendons is relatively large. It is easy to have adverse effects on the prestressed tendons during the tensioning process, causing the friction to increase abnormally. In order to minimize the loss of prestressed steel, optimization measures have been taken for the web prestressed steel tendons. Each segment is equipped with anchor connectors, which are arranged in a sequence of four segments per link.
The specific plan is as follows: After the first segment beam is stretched in place, organize anchor sealing operations, such as grouting; after completing the beam penetration operation of the second segment beam, make a single-end anchor head according to the requirements, and require it to be hung on the connecting head flange. place, equipped with reliable shields, steel rings and other related auxiliary devices, and can be grouted if correct; the connector is installed on the second section, and then the tensioning and anchoring work is organized there, and the jack pre-set there is removed and grout. Complete a single cycle of construction work in the above manner and proceed to the 4th section in sequence.
The cutting length of the steel strand is strictly controlled. The single-bundle end extrusion anchor head is in the form of an OVM single-end P anchor. In order to successfully complete the extrusion operation, it should be equipped with a YCW-20t jack.
Make preparations before extruding the end, that is, grind the end, and check the exposed length of the steel strand after extrusion. This part should be at least 20mm. The exposed parts of the two ends of the steel wire bushing should be as similar as possible, with 2 ~5mm is appropriate. After completing the construction of 2 to 3 pieces of anchor heads, a test must be organized in order to grasp the quality of the anchor heads in a timely manner.
(2) Strictly control the posture of the steel strands so that they pass through the anchor holes in parallel and cannot cross each other. The positional relationship between the anchor plate and the anchor pad is required to be on the same axis. The horn hole of the anchor pad should meet the requirements of cleanliness, and no cement slurry should be left; at the same time, check the contact area between the anchor pad and the anchor plate, which must be clean and flat, and use emery cloth to polish away any local floating rust and other debris.
Considering that the elongation exceeds the jack stroke during the tensioning process, the tensioning is carried out in an orderly manner according to the following process: 0→0.1σk→0.2σk→0.75σk→σk→load holding for 5 minutes (anchoring).
Control should be strengthened when prestressed steel tendons are stretched, with tension as the main control indicator and tested through elongation values. As the tensioning operation continues to advance, when it reaches the tensioning control requirement, the elongation at this time is detected. If the error with the design value is stable within ±6%, the tensioning operation can be ended. Otherwise, the tensioning needs to be suspended. Analyze specific causes and propose solutions.
3.3 Construction content of tunnel grouting and anchor sealing
3.3.1 Preparation work
After completing the tensioning operation, remove unnecessary exposed steel strands in a timely manner. This part is required to be 30mm and at least 1.5 times the diameter of the prestressed steel bars. After meeting this requirement, use cement mortar to seal the anchor head, and then use a sealing cover to set up an appropriate amount. The pipelines are designed to ensure that each channel is closely connected, and on this basis, it is equipped with vacuum pumps and other related devices. Before grouting, the anchor pad needs to be thoroughly cleaned to make it clean and flat, and then the asbestos sealing ring is installed in place, and the sealing cover and the anchor pad form a stable connection through bolt connection.
3.3.2 Try vacuuming
After closing the grouting valve, open the vacuum valve. At this time, the vacuuming effect can be achieved through the action of the vacuum pump, effectively cleaning the air in the duct. After processing, the vacuum degree is required to be stable at -0.06~-0.10MPa (maximize the vacuum degree as much as possible ), stop the pump for 1 minute after meeting this requirement, and detect the pressure drop at this stage. If the amplitude is within 0.02MPa, it means that the vacuum degree in the channel meets the requirements.
3.3.3 Slurry mixing
The slurry can be mixed and used. The duration from leaving the factory to being pressed into the hole must be ≤40mm, and it should be fully stirred before construction to ensure that the slurry has sufficient uniformity. Before slurry production, it needs to be idle for several minutes to make the inside of the mixer moist. The unloading must be done at one time, and mixing while unloading is not allowed. If the fluidity of the slurry is low, the fluidity cannot be increased by adding water. In addition, during the slurry mixing process, it is necessary to pay attention to the detection and control of the bleeding rate, regularly or irregularly detect the slurry and clarify its quality.
3.3.4 Grouting
Start the vacuum pump. After the vacuum degree meets the requirements, you can open the valve at the grouting end and continue grouting under the action of the grouting pump. Reasonably adjust the grouting pressure according to the actual situation. For vertical tunnels, 0.3~0.4MPa is more appropriate; during the construction of horizontal tunnels, the value should be appropriately increased and 0.5~0.7MPa is appropriate. Strengthen testing during construction. If the fluidity of the grout discharged from the other end of the tunnel is consistent with the fluidity of the poured part, it indicates that the grouting construction effect is good. After closing the grout outlet, a 3 to 5 minute stabilization period is given, and the whole process pressure should be maintained at 0.5MPa. . Start grouting from the lowest point to eliminate the influence of external factors as much as possible to ensure sufficient material supply and continuous grouting of the same pipeline. Completely record all data during the construction period, including grouting materials, grouting date, mixing time, vacuum degree, etc., to provide a basis for quality analysis.
3.3.5 Anchor sealing
After the grouting operation is completed, the box beams are deeply cleaned with high-pressure water to avoid laitance adhesion. At the same time, clean the dirt on the supporting pad, end face and other parts, and chisel the end face appropriately. High-grade mortar can be selected as the material for anchor sealing.
4 Conclusion
Prestressed post-tensioned concrete box girders are widely used in the field of bridge construction, but their construction is difficult and requires more attention to details and completion of each process in a reasonable manner, thereby improving the overall construction quality of the box girders and promoting bridge engineering. development of the industry.
Author: Zhou Shengfu (CCCC No. 4 Engineering Co., Ltd.)
This article was published in Issue 24, 2020, of "China High-tech" magazine